Our Approach
Gran Tierra is committed to conducting its business honestly, fairly and safely and has outlined these principles in a comprehensive, binding set of corporate policies. The Company carries out regular training annually to inform employees and contractors about all relevant policies and ensures compliance throughout the entire organization.
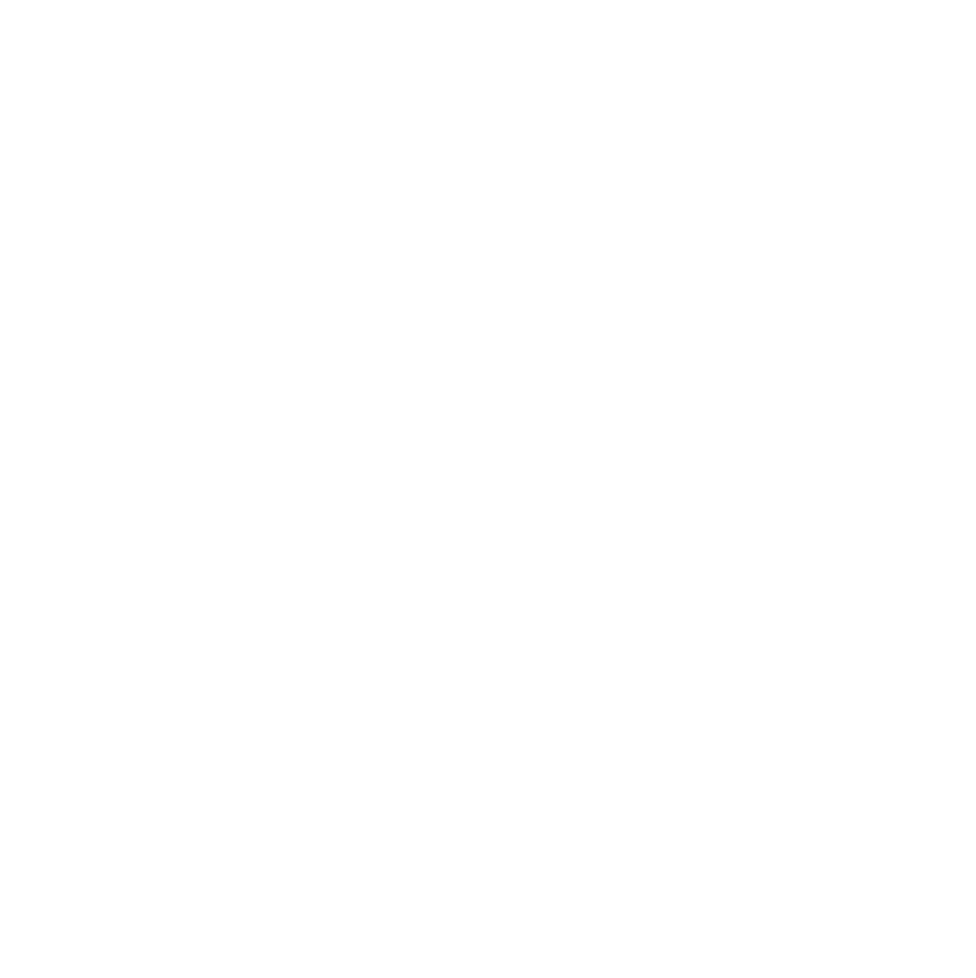
38%
OF THE 431 EMPLOYEES
at Gran Tierra Energy are
women versus the industry
average of 20%
Anonymous Whistleblower Reporting Program
Certificate Of Code Of Conduct By 100% Of Employees
Commitment To Ethical Conduct & Compliance
Human Rights Awareness & Training For Employees
Engage Board Of Directors With Majority Voting Standard
Annual “Say On Pay” Voting
SWIPE FOR MORE
Board Governance
The Gran Tierra Energy Board of Directors provide independent oversight of the company and are elected each year by Shareholders during our annual meeting. The Board is entrusted with the responsibility for overseeing the significant risks to which our business is exposed and ensuring there are processes in place to effectively identify, monitor and manage them. The Board delegates responsibility for the execution of certain elements of risk oversight to the committees to ensure appropriate expertise, attention and diligence. The committees oversee the relevant risk areas and report to the Board regularly.
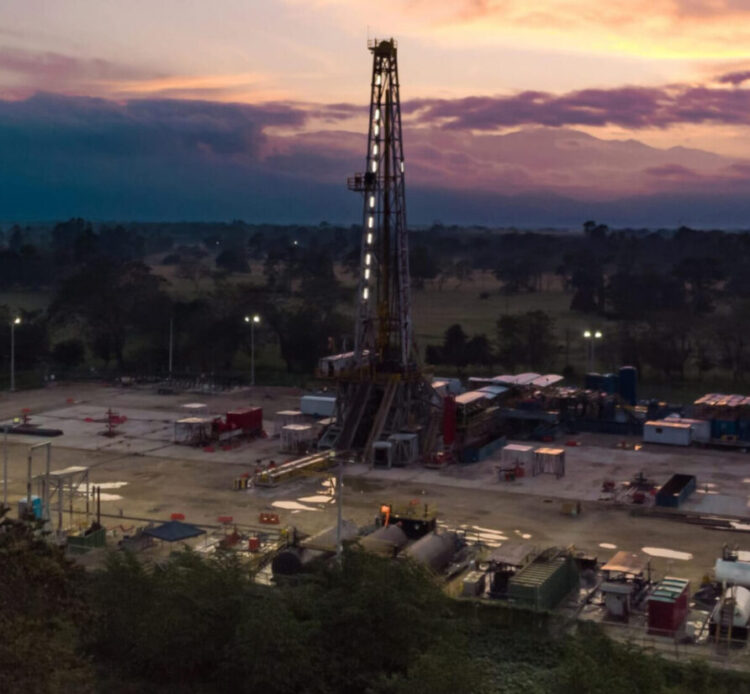
The Compensation Committee
is responsible for oversight of compensation-related risks, including reviewing management’s assessment of risks related to employee compensation programs.
The Health, Safety and Environment Committee
assists in overseeing the development, monitoring and effective implementation of systems, programs and initiatives to promote the management of health, safety and security at Gran Tierra and to address environmental, safety and operational risks.
The Nominating and Corporate Governance Committee
assists in overseeing governance related risks, including regulatory, reputation and other risks.
The Reserves Committee
assists in overseeing the risks related to the Company’s estimates of proved reserves of oil and natural gas.
The Audit Committee
oversees the accounting and financial reporting process and the audit of the Company’s financial statements, and assists the Board in monitoring the financial systems and Gran Tierra’s legal and regulatory compliance. The Audit Committee met four times in 2023 and at each meeting met with our independent auditors and the internal auditor, both privately and in the presence of management.
SWIPE FOR MORE
Learn more about our Commitment to Governance:
Governance Compliance
Gran Tierra’s Compliance Officer can be reached by email or telephone at +1 (403) 265-3221 ext: 2250.
Governing Policies & Guidelines for Ethical Conduct
Ethics Training
The Company requires completion of ethics training for all employees annually (Code of Business Conduct and Ethics every two years, and other specific risk-based training in the alternating years). In addition, all relevant employees, Senior Management, and the Board of Directors receive additional anti-corruption training. Course completion is monitored and audited by external auditors. In addition, the Compliance Officer’s receipt and handling of ethics and compliance complaints or concerns is audited by external auditors.
GTE’s 24-Hour Emergency Line
Whistle Blower Hotline
Whistle Blower Hotline link will take you to Ethicspoint, where you can anonymously and confidentially communicate any issues and concerns.